Mr. Yoda: From what I understand, the SU-3200 and SU-3300 received the GVA in large part because they not only reduce customer CoO but also significantly reduce environmental impact. What were the factors that led to their development?
Mr. Tanaka: Miniaturization of semiconductor is continually being developed in order to increase how many integrated circuits can be accommodated per unit area. Miniaturization means changing the line width, and this creates a major challenge for semiconductor device manufacturers in the form of higher production costs. Of course, having a Miniaturization will improve productivity, but if the cost of chemicals and other expendables used in the production process, as well as electricity and other energy costs, cannot be lowered, the increased productivity will not lead to any improvement in the necessary CoO. Improving CoO helps improve energy-saving performance, which in turn leads to a reduction in environmental impact.
Mr. Yoda: This equipment is really revolutionary in terms of reducing liquid chemical waste.
Mr. Tanaka: When you miniaturization of the semiconductor, the amount of chemicals needed to remove all of the contaminants (mask material, dry process residue, particulate matter) from the wafer during the cleaning process increases significantly. And because sulfuric acid comprises a large percentage of the chemicals used, the cost of neutralizing the liquid chemical waste is also significant. With the SU-3200 and SU-3300, factors such as chemical temperature and cleaning method were optimized to reduce the amount of chemicals used, thereby contributing to an increase in productivity and energy-saving performance, which improved CoO by the amount demanded by the customer. We have also worked to reduce the amount of water that this equipment uses.
Mr. Yoda: My company manufactures lead-acid batteries, which also require sulfuric acid as part of the production process. So I truly understand just how much water, chemicals, and energy are required for post-process treatment of sulfuric acid waste. From a business standpoint, reducing the amount of sulfuric acid is a real win-win situation, as it both improves CoO and reduces environmental impact.
Mr. Tanaka: Customers have responded quite well, and this has resulted in a lot of orders. In terms of next-generation semiconductor manufacturing, the superior environmental performance of this equipment has earned it inclusion within the PoR (process of record [the core process for mass production]), which is a major accomplishment.
Pursuing Enhanced Corporate Value through Environmental Management
Business-driven Initiatives for the Realization of a Sustainable Society
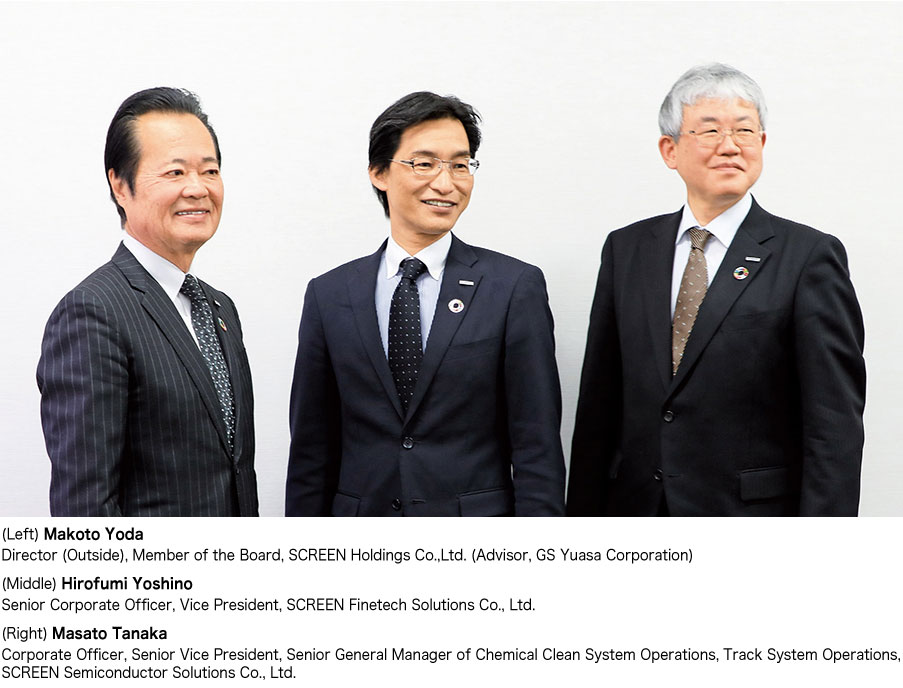
Environmental management aimed at ensuring environmentally friendly business practices is becoming an increasingly important part of sustainable corporate growth. In this special feature, we look at how the SCREEN Group is integrating environmental management into its business, focusing specifically on SU-3200/SU-3300 single wafer cleaning equipment, which received the in-house Green Value Award (GVA)*1 for its contribution to reducing both customer CoO*2 and environmental impact, and the RT Series roll-to-roll coater/dryer used in fuel cell and lithium-ion battery production.
※1 CoO(Cost of Ownership): | A criterion used in evaluating the economic efficiency of semiconductor manufacturing capital investment and operations. Product cost is calculated based on the price, productivity, reliability, yield, etc., of the production equipment. |
※2 Green Value Award: | An in-house award program that recognizes those sections within the SCREEN Group whose business activities, products, or services have made outstanding contributions to EHS (environment, health, and safety). Judging is carried out based on six criteria: innovativeness, originality, practicality, continuity, economic effect, and user evaluation. |
Improving CoO Means Reduced Environmental Impact
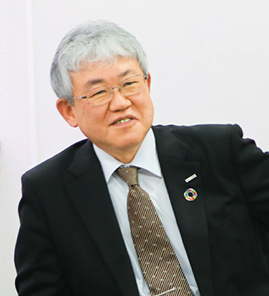
Corporate Officer, Senior Vice President, Senior General Manager of Chemical Clean System Operations, Track System Operations,
SCREEN Semiconductor Solutions Co., Ltd.
Developing Systems That Facilitate Fuel Cell Innovation
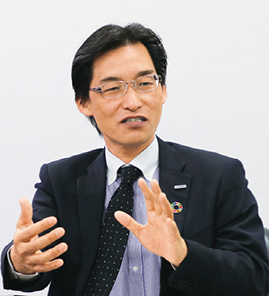
Senior Corporate Officer, Vice President, SCREEN Finetech Solutions Co., Ltd.
Mr. Yoda: FT has also been developing environmentally friendly advancements to meet the evolving demands of display manufacturing.
Mr. Yoshino: The evolution of LCD panels in the display industry has increased glass size roughly 100-fold between the first generation (G1) and the current, 10th generation (G10). However, there has not been a comparable increase in energy required to run the display manufacturing equipment. Because ways to reduce water, chemicals, and electricity usage are continually being found, the 100-fold increase in screen size has required only about a two-fold increase in electrical power consumption and almost no increase in chemical usage. It is essential that we maintain an extremely costconscious mindset, and this sort of approach is also beneficial to the environment.
Mr. Yoda: The environmentally friendly initiatives undertaken by FT also extend to renewable energy promotion via its new business, specifically the development and launch of a roll-to-roll coater/dryer (RT Series), which facilitates fuel cell and lithium-ion battery manufacturing. How does the RT Series compare with conventional systems?
Mr. Yoshino: The RT Series comes in two varieties: one for lithiumion batteries and one for fuel cells. The lithium-ion battery system takes up roughly 40% less space and uses roughly 20% less power than conventional systems. These benefits have been well received by customers, resulting in increasing sales. The fuel cell system is attracting significant interest thanks to the fact that it increases productivity roughly 10-fold compared to conventional systems. It is also being adopted for domestic-use fuel cell (ENE-FARM) manufacturing.
Mr. Yoda: Due to the fact that they emit no greenhouse gases, fuel cells are being touted as a game-changer that will make it possible to achieve the Paris Agreement’s long-term target of keeping a global temperature rise well below 2°C above pre-industrial levels. However, a major obstacle to the widespread adoption of fuel cells is their production cost. Is it accurate to say that the RT Series helps to reduce that cost?
Mr. Yoshino: Yes. As manufacturers of systems and equipment offering superior productivity, we take great pride in our efforts to foster innovation that directly contributes to the creation of a fuel cell market.
Towards the Creation of a Decarbonized Society
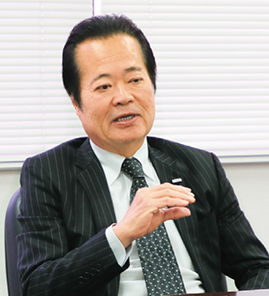
Director (Outside), Member of the Board,
SCREEN Holdings Co.,Ltd.
Mr. Yoda: A great deal of attention is being focused on electric automobiles as a means of reducing greenhouse gas emissions. However, electric vehicles alone will not be enough to achieve the Paris Agreement’s targets. There will need to be significant reductions among the major greenhouse gas-producing industries, particularly the power industry. The SCREEN Group is working to not only reduce our own greenhouse gas emissions via our SDGs initiatives, we are also offering equipment on the market that contribute to increased production efficiency and reduced greenhouse gas emissions for the companies that use them. I think this is truly fantastic.
Mr. Tanaka: As a systems and equipment manufacturer, we pursue a CIP (continuous improvement process) that is aimed at developing a concrete roadmap for helping both ourselves and our customers deal with resource depletion, global warming, hazardous materials, and other challenges. The next generation of business is inextricably linked with the pursuit of environmental management, including reducing liquid chemical usage, promoting recycling, finding environmentally friendly substitutes, conserving energy, accommodating energy-efficiency product laws and regulations, and eliminating the use of prohibited materials.
Mr. Yoshino: In Europe and America they are implementing a renewable energy-driven power-to-gas approach to achieving a decarbonized society, which involves hydrogen purification, storage, and use. Widespread adoption of fuel cells is the key to making this approach work. I firmly believe that our systems, equipment, and technology can contribute to this significantly. We are working on developing systems and equipment that will boost productivity even further.
Mr. Yoda: The inventions and technologies of the 20th century have enriched society by making our lives easier, but they have also contributed to greater environmental contamination, such as the pollution created by microplastics. In the 21st century, we need an industrial revolution that will solve these problems of garbage and waste. The SCREEN Group is able to significantly contribute to the creation of a decarbonized society, and I expect that our efforts will only grow larger as time goes on.
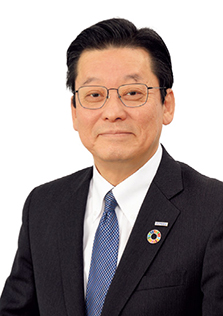
Managing Director, Member of the Board, Chief Officer of Sustainability Promotion,
SCREEN Holdings Co.,Ltd.
This year’s GVA-winning equipment, the SU-3200 and SU-3300, significantly reduce the environmental impact of the semiconductor manufacturing process. And the RT Series contributes to the realization of a decarbonized society by dramatically improving lithium-ion battery and fuel cell manufacturing productivity. Through the development of such equipment, the SCREEN Group is working hard to address ESG issues. And I believe that we will continue to make steady progress in addressing them thanks to the tireless efforts of each and every one of our employees and their commitment to meeting the exacting demands of our customers while helping to build a sustainable society. Consideration for the environment and for society when conducting business is a key aspect of corporate value. In areas of our business, I look forward to continuing to both meet and anticipate our customers’ needs, to helping address environmental needs and other societal needs, and to discovering new business opportunities in doing so.