SCREEN's Core Technologies
The SCREEN Group possesses core technologies in three key areas: surface processing,
direct imaging and image processing. Each of these areas includes its own foundational technologies,
which we have progressively expanded into the semiconductor, print, display, PCB and other markets.
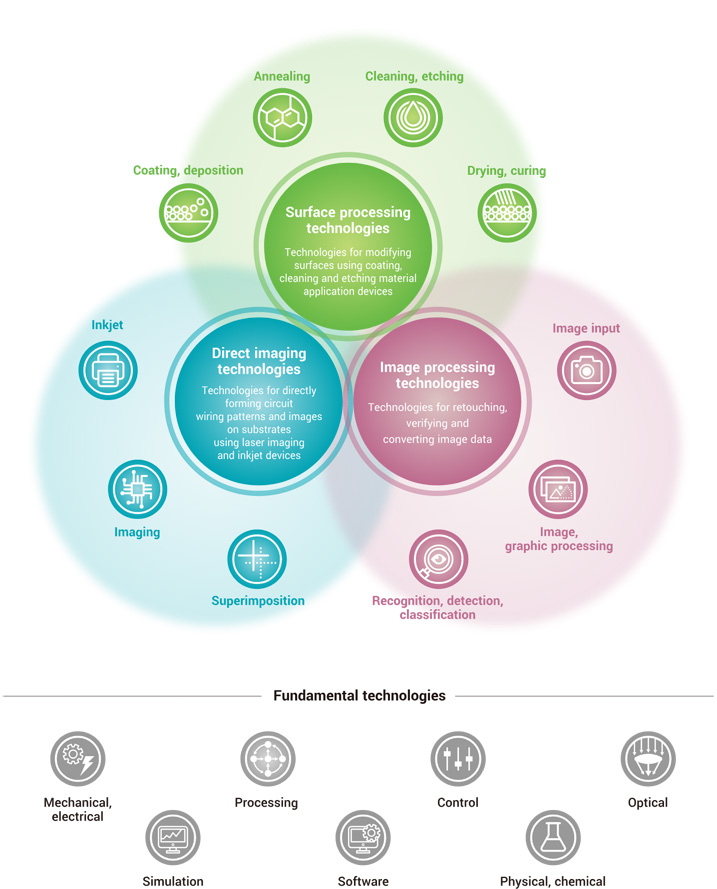
- Surface processing
technologies - Technologies for modifying surfaces using coating, cleaning and etching material application devices

Cleaning, etching
These technologies have been developed for the semiconductor field, where they are needed to perform high-precision cleaning and processing of minute patterns measuring just tens of nanometers, as well as the display field, where they are used in the manufacture of large size glass substrates of two or more meters in length. Cleaning and etching are key technologies supporting the production of cutting-edge semiconductor and display components.
- Glass cleaning and etching technologies for large size displays
- Single wafer cleaning and etching technologies for semiconductor devices (separate processing of individual wafers)
- Batch cleaning and etching technologies for semiconductor devices (group processing of multiple wafers)
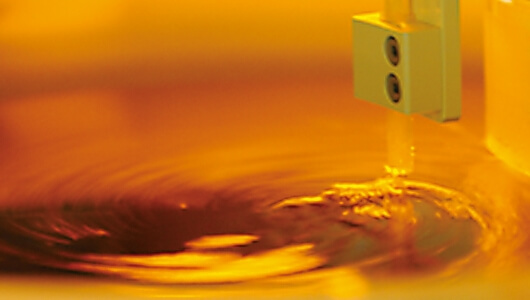
Coating, deposition
Coating and deposition technologies are used to uniformly apply chemicals to semiconductor substrates and glass substrates for large size displays at micron or submicron thicknesses. We possess a wide range of such technologies, from wet processes that use spin coating or slit nozzles to dry processes that employ plasma discharge. Coating can also be performed on a variety of materials from hard substrates through to flexible films.
- Coating technologies for high-viscosity liquids (materials for lithium-ion batteries, etc.)
- Slit nozzle coating technologies (displays)
- Spin coating technologies (semiconductors, displays)
- Coating technologies for film rolls (metals, resins)
- Plasma deposition technologies for large size substrates
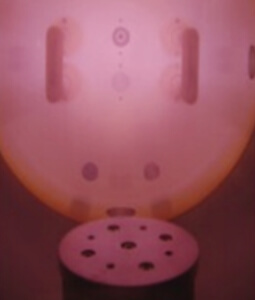
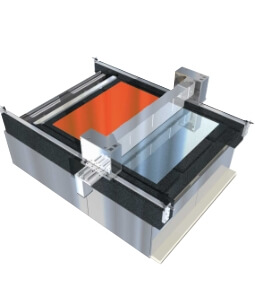
Drying, curing
Drying and curing are an essential part of a set of technologies that also includes cleaning, etching and coating. Our technologies prevent damage to the electrical performance of circuits or the structures of minute patterns when drying semiconductors. They also maintain highly precise, uniform film thicknesses and quality when performing drying and curing after coating. We also supply a wide variety of composite technologies that can be used for specialized applications.
- Spin drying technologies (semiconductors)
- Air knife drying technologies (displays)
- Low pressure drying technologies (semiconductors, displays)
- Dry air drying technologies (semiconductors, displays)
- Ultraviolet and infrared curing technologies (displays)
- Roll-to-roll drying technologies (lithium batteries, fuel cells)
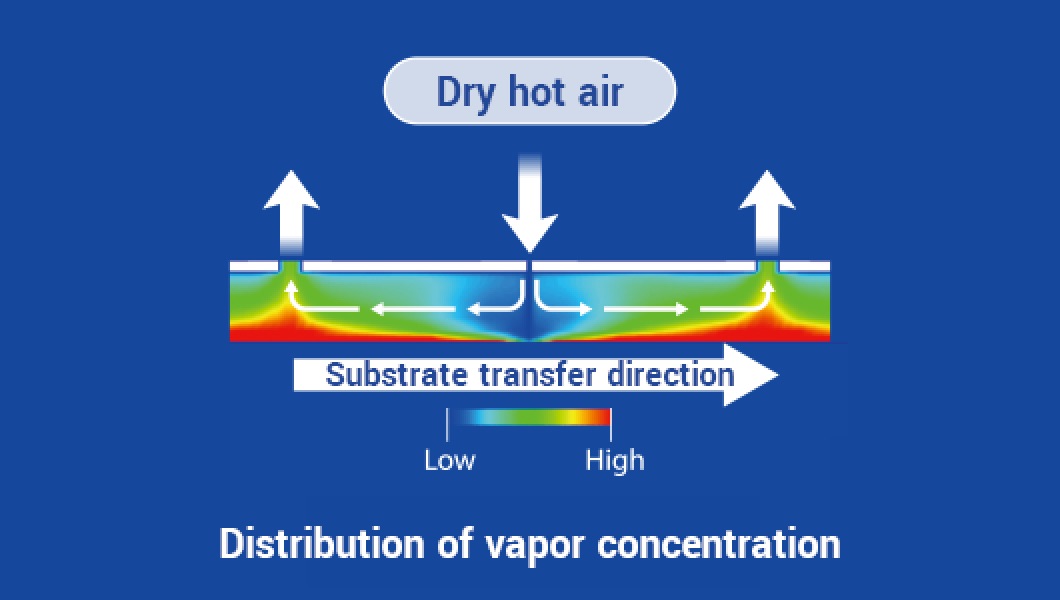
Annealing
This technology uses flash, laser or other light sources to instantaneously heat the surfaces of substrates. The sudden application of heat energy onto the substrates is what gives semiconductors their excellent electrical characteristics.
- Rapid annealing technologies (thermal modification)
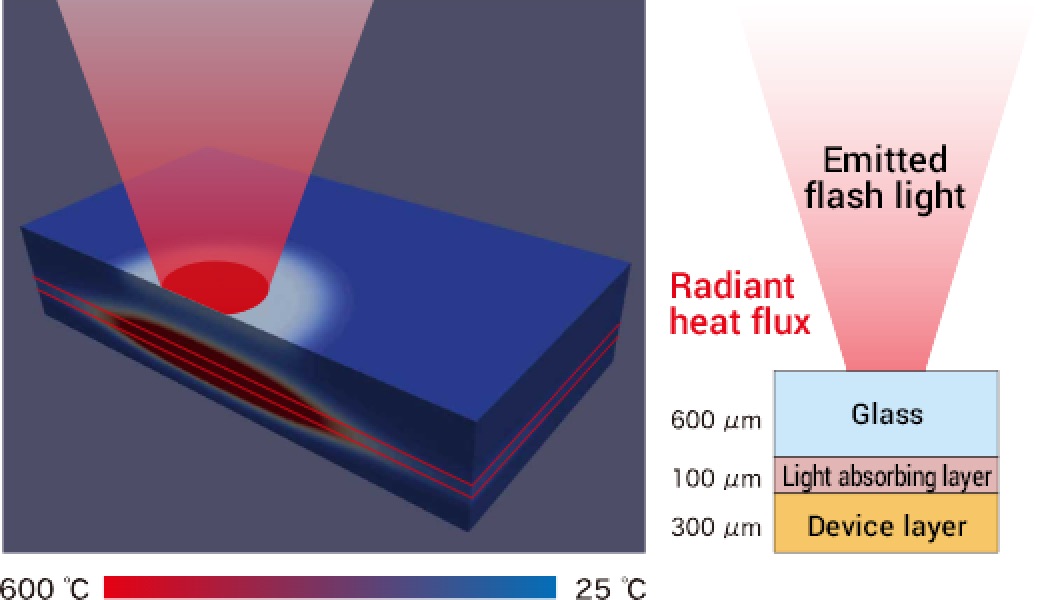
- Direct imaging
technologies - Technologies for directly forming circuit wiring patterns and images on substrates using laser imaging and inkjet devices

Inkjet
Inkjet devices are able to print directly onto media such as paper and film. A wide variety of processing technologies including halftone screening and data manipulation can be used on print data to increase output quality and speed.
Our systems feature a combination of technologies that support data processing, optimization of ink control and quality evaluation. They provide greater flexibility in data application, allowing them to handle work ranging from mixed, small lot jobs to high volume print runs.
- Ink droplet control technologies (control of discharge timing, ink volume)
- Halftone, color management technologies
- Print data control technologies
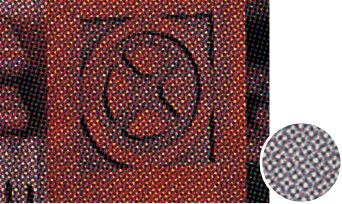
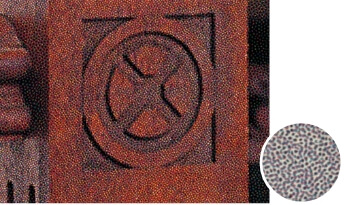
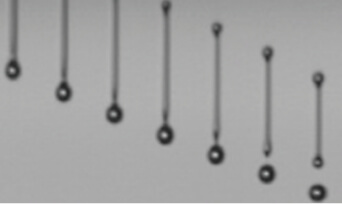
Imaging
Imaging technologies use light sources such as lasers and LEDs with optical modulators to expose data directly onto media coated with photosensitive material. The approach provides a greater degree of flexibility in data processing.
In the printing field, the technique is used to create printing plates (CtP process) while in the semiconductor and PCB fields, it is used to form circuit wiring on substrates. Extremely precise, high-quality imaging can be achieved using our own proprietary optical modulators (with GLV™ technology), or devices from other companies, in combination with optimized optical and control systems that maximize their performance.
- Direct imaging technologies for PCBs
- Direct imaging technologies for semiconductor wiring
- Direct imaging technologies for printing plates (CtP)
- Technologies for optical modulator production and imaging control
- Control technologies for imaging data
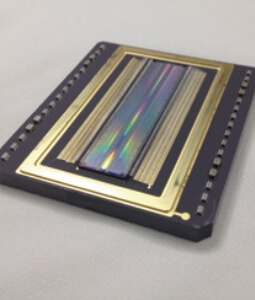
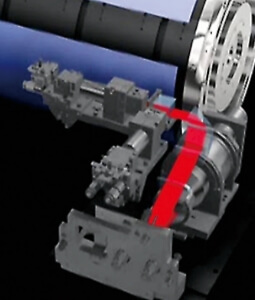
Superimposition
This field brings essential inkjet and imaging technologies together as a set. Combining these technologies allows multiple different types of data to be superimposed while moving the media and inkjet or imaging heads relative to each other. The approach enables the execution of highly precise printing or imaging.
An array of technologies are employed to read the data from already printed or imaged media and improve layering accuracy. They include head positioning, data processing, ink droplet control, and laser and optical modulator control technologies.
- Superimposition imaging technologies (alignment technologies)
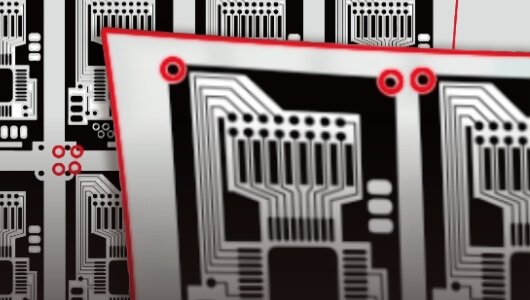
- Image processing
technologies - Technologies for retouching, verifying and converting image data

Image input
Image input technologies are responsible for the control of illumination (visible, infrared, laser light, etc.), optical design (lens design, simulation) and imaging sensors (line, area sensors, etc.) as well as the optimization of data transfer required for different types of image processing.
- Image sensing technologies (illumination, capture)
- High-speed data communication technologies
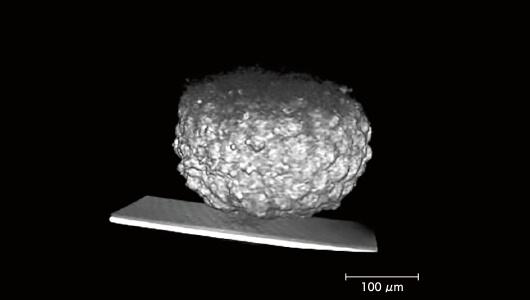
Image, graphic technologies
Image and graphic technologies perform processing of input image data (including tone conversion, filter application, and vectorization of bitmap data) in preparation for the recognition, detection, classification and measurement of target items.
- Image processing technologies, Graphic creation technologies
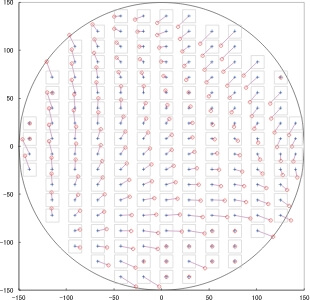
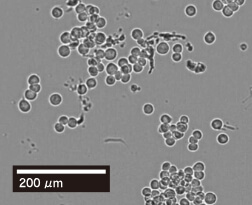
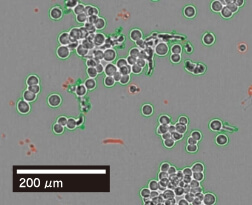
Recognition, detection, classification
These technologies compare input images with reference data, allowing the recognition, detection and classification of target items. They are used in applications such as the detection of defects in circuit wiring on PCBs and semiconductor substrates, the detection of unevenness in surface coatings and the visual inspection of in-vehicle components.
Our classification procedures make use of advanced machine learning, helping to increase both accuracy and automation. Automation of inspection processes leads to significant improvements in throughput, cost performance and reproducibility, resulting in more consistent product quality.
- Unevenness detection technologies
- Visual inspection technologies for circuit pattern boards
- Defect classification technologies (machine learning)
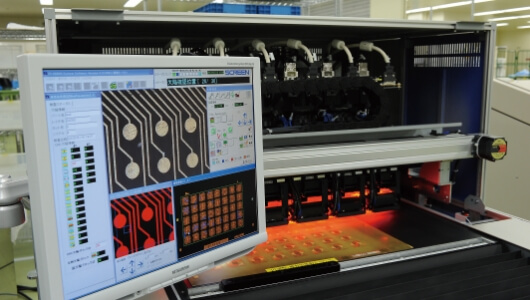
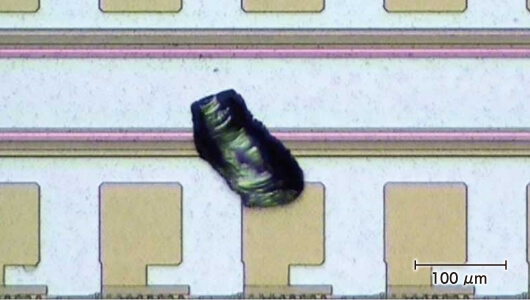