【人と仕事】
Project Story
【新規事業】
プロジェクトストーリー
SCREENグループが世界に誇るコア技術を用いて、
次の世界一を目指す新規事業がどのようなプロセスを経て
誕生したのかを辿っていきたい。
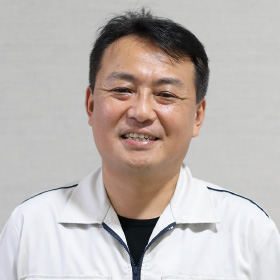
プロジェクトリーダー
T.Yさん
新規事業統轄部
技術部 プロセス技術課
2001年入社
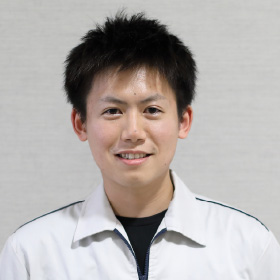
電気制御
O.Hさん
新規事業統轄部
技術部 電気技術課
2018年入社
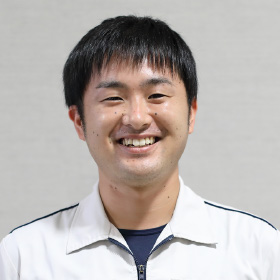
機械設計
A.Nさん
新規事業統轄部
技術部 機械技術課
2014年入社
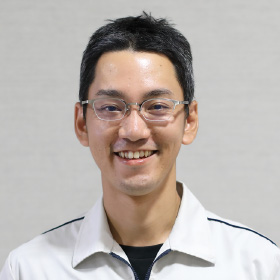
プロセス技術
K.Tさん
新規事業統轄部
技術部 プロセス技術課
2007年入社
将来性が期待される燃料電池の量産化を実現。
不可能を可能にした画期的な装置は、
市場拡大を加速させ、ビジネスの可能性を広げる。
Phase.1
産学官連携プロジェクトの発足直後に
難易度の高さを知り、窮地に立たされる
2013年、将来のSCREENの主力となる事業を立ち上げるためのプロジェクトが発足された。「エネルギー関連の新規事業」というミッションを受け、各部門から抜擢された技術者4人は、社内外に足を運び、あらゆる観点から市場リサーチを進め、「燃料電池の量産装置」に着目した。
エネルギー供給の安定化や地球温暖化対策といった課題を解決できる燃料電池の市場は、2030年には6兆円を超える規模に拡大すると予測され、特に燃料電池自動車や家庭用燃料電池(エネファーム)は急速に普及が進んでいる。その一方で、量産化に向けた効率化やコスト低減を実現する新たな技術が求められていた。SCREENには、世界シェア8割を誇るコーター・デベロッパー(フラットパネルディスプレー製造装置)で培った塗布・乾燥技術がある。その表面処理技術を生かせると考えたのだ。しかし、新しい装置の開発には巨額な資金が必要である。そこで燃料電池研究センターを備える大学に共同研究を持ちかけ、産学官連携のプロジェクトとしてNEDO(国立研究開発法人新エネルギー・産業技術総合開発機構)に助成事業の申請をすることにした。早速、自動車メーカーなどを訪問し、現状の課題やどんな装置を求めているのかを綿密にヒアリング。そして自動車や家庭用に普及する固体高分子型燃料電池の電解質膜に電気触媒(溶剤)を直接塗布・乾燥し、ロールtoロール方式で連続生産する装置の開発をNEDOに提案して採択された。しかし、喜んだのも束の間、大手自動車メーカーでも実現できない、非常に難易度の高い技術であることを知ったのだった。
この電解質膜は厚さ数ミクロンという高分子の薄膜のため、溶剤を塗布するとシワになったり、溶けてしまう。わかりやすく例えると、粉薬などを包む薄いオブラートの両面に溶液を塗るようなものだ。リーダーのT.Yは「業界のことをまったく知らない私たちは、できると思っていましたが、あまりにもハードルが高い。NEDOの助成事業でなかったら1年で諦めていたかもしれません」と語る。会社のメンツもあるので止めることはできない。プロジェクトは最初から窮地に立たされた。

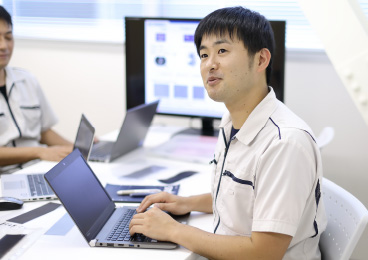
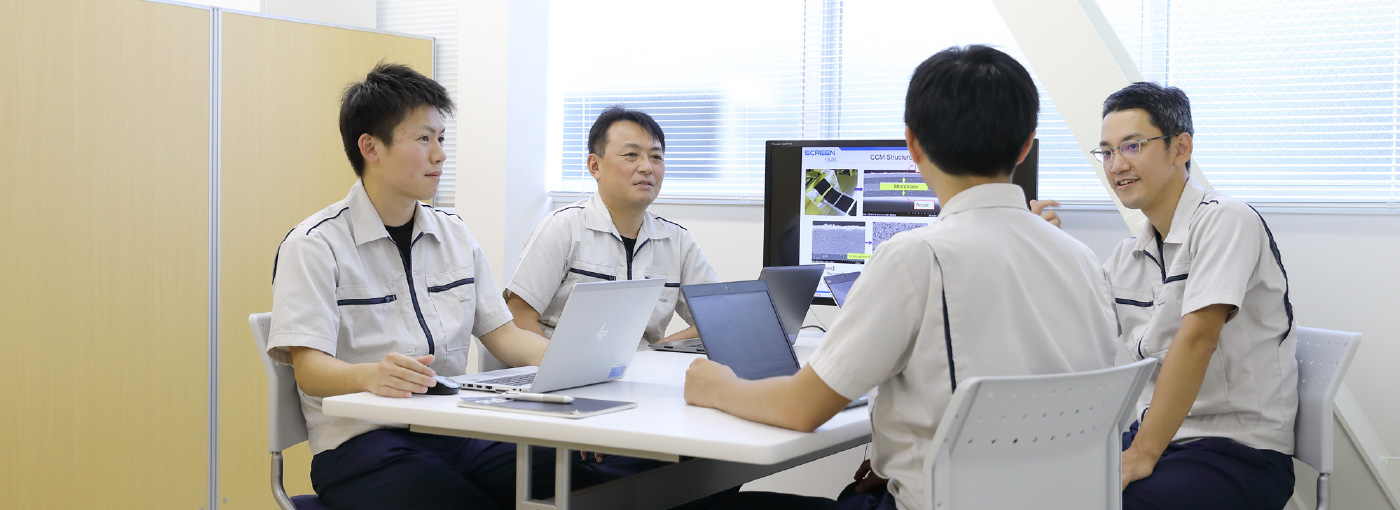
Phase.2
紆余曲折を経て完成した試作装置を
購入したいという企業が現れた!
プロジェクトはリーダーのT.Yが全体を統括し、プロセス技術のK.Tが装置の設計から製造までの全工程をデザイン。その要求に基づいて機械設計のA.Nと電気制御のO.Hが設計や製品化に携わった。リーダー以外は全員が20代の若手だ。
まずは治具部品の製造開発に取り組み、その部品を組み立てたパイロット装置で試作をし、最後に実際の製品を量産化して不具合の調整などを行う。最初の治具部品の製作で苦労したのは、機械設計のA.Nだった。
「数ミクロンの膜に溶剤を塗布してもシワなどが無い高精度治具の開発が必要でしたが、引き受けてくれるメーカー探しに苦戦しました。今でもこの部品をつくれるのは、日本でも限られています」
1年をかけて治具部品をそろえ、2年目にはパイロット装置を稼働させた。このフェーズで要の役割を担うのは、電気制御のO.Hだ。ミクロン単位で均一に塗布する動作、その後の乾燥工程でも温度などの条件を一定に保つための制御に試行錯誤した。大きな障壁となったのは、試作が難しいことだった。
「電解質膜に塗布する溶剤は白金を含むため、30分の稼働テストにかかる材料費は数百万円。試作せずにデバックしなければいけない条件のなか、プロセス技術のK.Tからは部品の改良や制御の精度向上の要求が続きました」
一方、プロセス技術のK.Tは、電解質膜に塗布する溶剤について、膜が溶けにくいものをチューニングして装置とセットで提供することで付加価値を高めた。
「トライ&エラーを繰り返し、いい結果が出たら大学に解析依頼をして根拠の裏付けをとってもらう。当社だけでは到底無理だったでしょう」
このような4人の努力により、パイロット装置の大枠が完成し、この装置を購入したいという企業が現れた。しかし、品質管理ができるように検査装置を組み込むという条件つき。もちろん、そのような装置をつくった経験はない。プロセス技術のK.Tは検査装置のレイアウトから品質管理に必要な項目の洗い出し、生産工程を綿密に検討して少しでも要求に近づけるように顧客と技術者の橋渡しを行った。

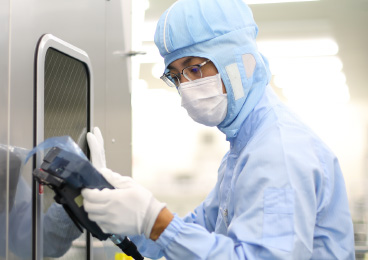
Phase.3
顧客と二人三脚で取り組むことで
当初の性能を上回る装置開発に成功
検査装置を組み込んだ燃料電池の量産装置が完成した後、量産化によるテストを行ったが、改良や調整には1年の歳月を費やした。顧客の工場に装置を据え付け、実際に生産ラインを動かしてからは、今まで以上に要求レベルが高まったのだ。製品の精度はもちろんのこと、装置のセットアップから操作性、稼働後の不具合など想定外の課題が見つかり、この最終工程が一番苦労したとメンバーたちは語る。一つ一つ原因を追求して改善を続け、うまく動かないときはその場で装置を解体し、代わりの部品を用意して組み立てた。そんな厳しい要求が続く一方で、彼らの迅速で真摯な姿勢が顧客との信頼につながり、一緒にオンリーワンの装置をつくる技術者としての絆も育まれていった。
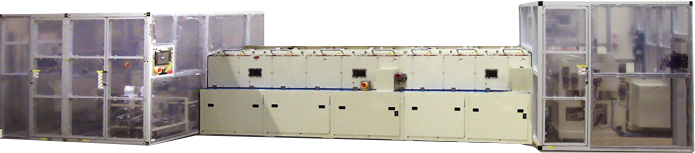
そして2016年、遂に世界に向けてリリースされた。この「RTシリーズ」は、従来の10倍以上の生産性を誇る画期的な燃料電池の量産装置。さらに電極寸法や欠陥、膜厚などの検査装置を組み込むことにより、品質管理が同時に行えることも注目された。
「検査装置付きの要望を聞いたときは躊躇しましたが、今までにない新しい装置だからこそ、お客さまと議論を交わしながら一緒にものづくりができました。また、長期にわたりプロジェクトに専念し、着実にステップを踏めたのが成功の要因。既存のシリーズよりも数倍の労力が必要ですが、じっくりと腰を据えて開発させていただけた会社に感謝するとともに非常に面白かったです」とリーダーのT.Yは、この7年間を振り返る。しかし、プロジェクトは終わったわけではない。歩留まり率の向上をはじめ、装置の完成度を高めていくこと。さらに後工程の装置の開発にも着手し、ラインアップを増やしてビジネスの拡大を図っていく。その取り組みは、燃料電池業界を活性化し、市場拡大を加速させていくであろう。
SCREENでは、常に複数のプロジェクトが動いている。しかし、製品化までたどり着くのはほんのひと握り。技術者にとって「新規事業の成功体験」は、何にもかえがたい大きな収穫であり、スキルアップと同時に仕事への自信やプライドを育んだ。そんな彼らは、これからも苦労や困難に立ち向かう挑戦者であり続けるであろう。
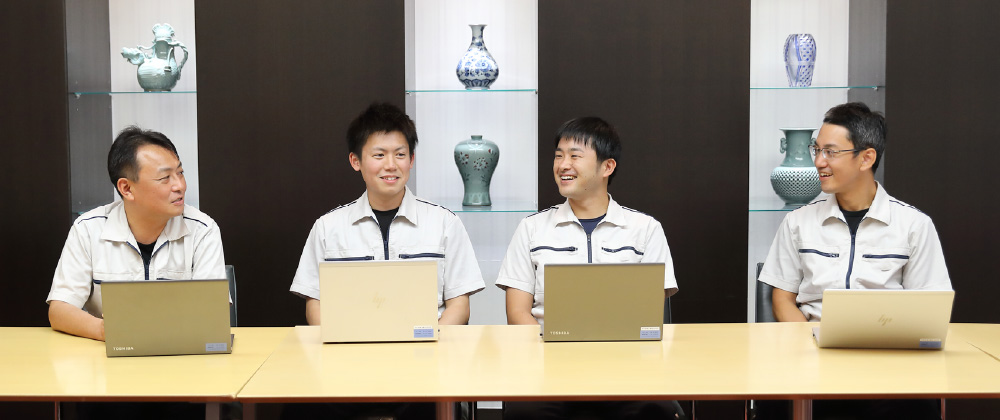